在現代塑料制品生產中,著色工藝已成為提升產品附加值的關鍵環節。隨著技術進步和環保要求提高,塑料著色技術正朝著更高效、更環保的方向發展。
創新著色技術引領行業發展
當前塑料著色領域已形成多元化的技術路線。其中,預分散色母粒技術因其優異的分散性和色彩穩定性,成為高端制品首選方案。該技術通過將顏料與載體樹脂預先復合,有效解決了傳統干粉著色存在的粉塵污染問題。值得注意的是,液體著色系統在精密注塑領域展現出獨特優勢,其精確的計量控制可實現0.5%的色彩偏差,大幅提升了產品合格率。
據色母粒產業網了解,近年來在線著色技術取得突破性進展。通過智能化計量系統與擠出設備的聯動,生產企業可實現不同顏色產品的快速切換,將換色時間縮短至傳統工藝的1/3,顯著降低了生產損耗。這種技術特別適用于多品種、小批量的定制化生產需求。
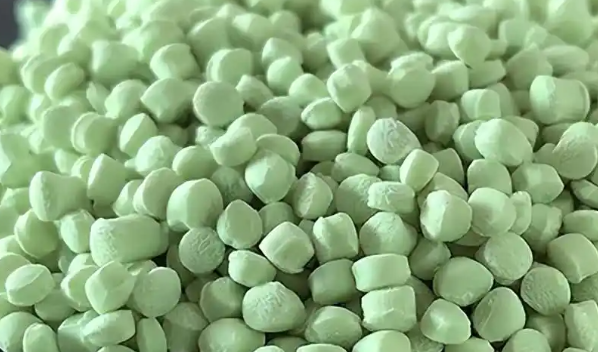
褪色難題催生新型穩定體系
塑料制品的耐候性能直接影響其使用壽命和市場價值。研究顯示,紫外線輻射是導致戶外用塑料制品褪色的首要因素,約占總褪色案例的65%。為此,材料專家開發了復合穩定劑系統,將紫外線吸收劑與受阻胺光穩定劑(HALS)協同使用,可使塑料制品的戶外耐候壽命延長3-5倍。
在化工新材料領域,納米級二氧化鈦和氧化鋅等無機紫外線屏蔽劑正獲得廣泛應用。這些材料通過物理反射原理,在塑料表面形成保護屏障。實驗數據表明,添加2%納米氧化鋅的PP材料,在經過1000小時紫外老化測試后,色差變化(E)可控制在1.5以內。
環保法規推動著色劑革新
隨著全球環保法規日趨嚴格,傳統的含重金屬顏料正逐步被淘汰。歐盟REACH法規最新修訂版已明確限制21種有害著色劑的使用。這一趨勢促使企業加速開發新型環保著色體系。目前,有機顏料微膠囊化技術和生物基染料已成為研發熱點,部分產品已通過食品接觸材料認證。
在汽車內飾件等高端應用領域,耐遷移性成為衡量著色劑品質的重要指標。通過分子結構改性和表面處理工藝,新一代著色劑可將遷移率降低至0.01mg/cm2;以下,完全滿足汽車行業VDA270標準要求。這些技術進步為塑料制品開拓了更廣闊的應用空間。